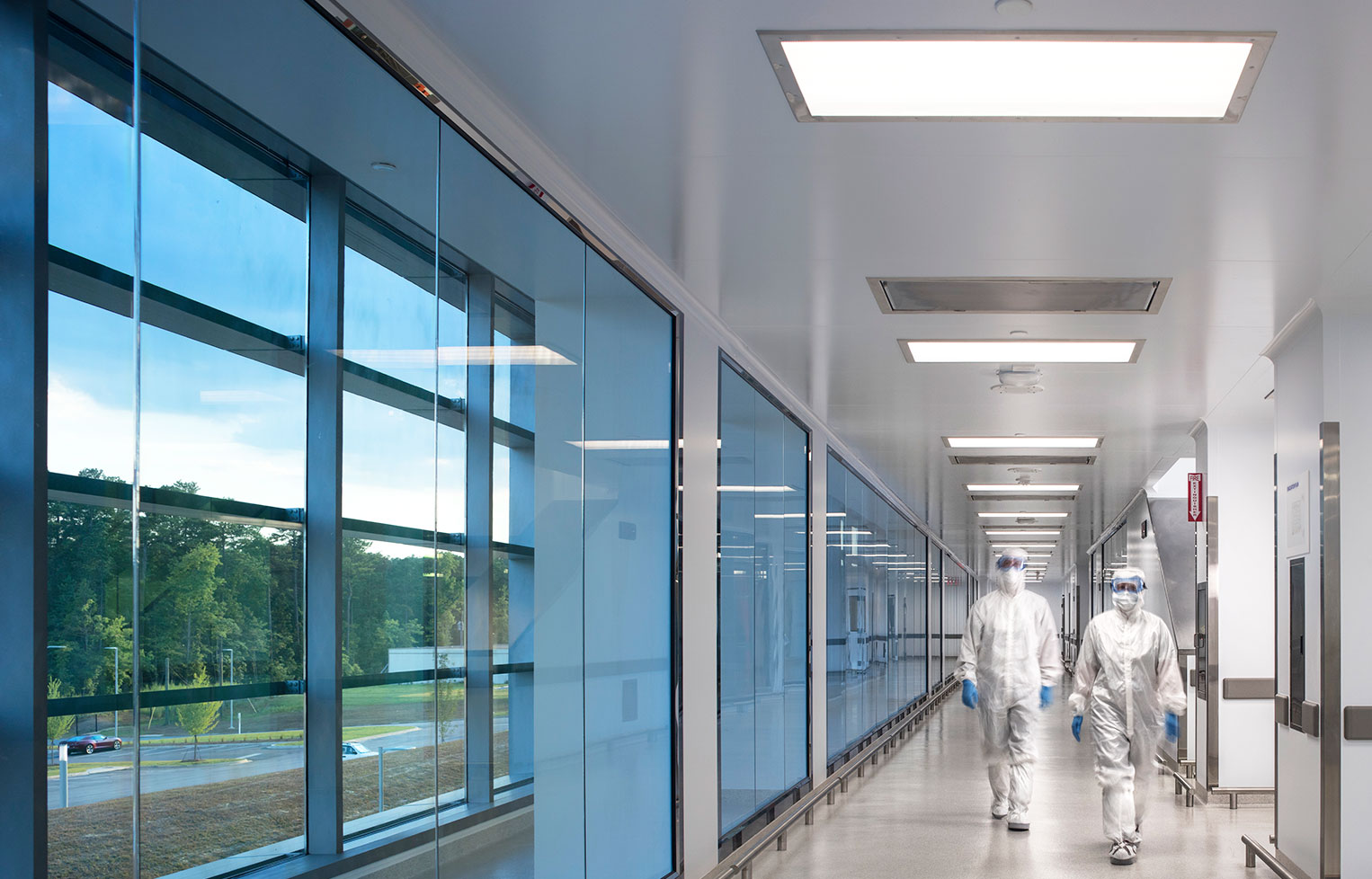
Traditional, stick-built cleanroom construction is labor intensive, relies on complex detailing, and requires experienced, qualified installers for successful installation. This type of construction also generates significant dust and airborne contaminants that are difficult to eradicate once construction is complete. All contractors and tradesmen must be trained and certified in clean construction protocols to limit dust generation.
Alternatively, prefabricated, modular cleanroom systems are available that are specifically tailored to aseptic environments and can reduce construction schedules, increase flexibility for the facility, and help expedite the validation/closeout process.
The Case for Prefabricated Cleanroom Construction
Traditional, stick-built cleanroom construction is labor intensive, relies on complex detailing, and requires experienced, qualified installers for successful installation. This type of construction also generates significant dust and airborne contaminants that are difficult to eradicate once construction is complete. All contractors and tradesmen must be trained and certified in clean construction protocols to limit dust generation.
Alternatively, prefabricated, modular cleanroom systems are available that are specifically tailored to aseptic environments and can reduce construction schedules, increase flexibility for the facility, and help expedite the validation/closeout process.
Section 13.6 of the NIH Design Requirements Manual (APF Design Requirements: Architectural) states that "Monolithic composite panelized systems are preferred" and that "modular cleanroom wall systems are also preferred." However, not all prefabricated cleanroom systems are created equally. There are many features and characteristics to consider when evaluating prefabricated cleanroom systems and components.
The cleanability of the panel system is one consideration. The wall and ceiling finishes in aseptic facilities must be smooth, cleanable, and impervious to the regular use of cleaning agents. All field joints must be cold-welded or sealed, and the quantity of joints should be kept to a minimum. Sealant joints require routine inspection and maintenance over the life of the facility to ensure there are no cracks or crevices where contaminants can collect.
The interface of the resinous flooring system with the wall panels should also be taken into consideration. Some panel manufacturers have developed a floor track system that is recessed from the face of the panel. This allows for a flush, clean condition at the top of the integral coved base rather than a screed ledge and/or a sealant joint. Small ledges are another surface to clean and should be avoided to the extent possible within aseptic facilities.
Ceiling systems should be fully sealed, self-supporting, should limit deflection and sagging, and should be designed for room pressurization. Other ceiling considerations include the interface of light fixtures, fire suppression devices, access panels and the viability of above-ceiling walkability.
Modular wall manufacturers can more effectively expedite construction schedules when folded into the team early in design. This early engagement helps the manufacturer produce better coordinated fabrication drawings and speeds up the review and approval process. The manufacturer can become an extension of the design team and can help ensure that a high-quality, aseptic environment is realized.
Flad Architects has worked with several of the leading manufacturers of prefabricated cleanrooms, and we are well-versed in the features and advantages of these systems, including assembly methods, detailing, and MEP integration. We assist clients in the evaluation of manufacturers based on reputation, as well as features that are important to them (for example; cost, durability, or speed of construction), so that they can realize the full benefits of what these systems offer.